Products >> Sodium_Hypochlorite_Generator (Seawater) >> offshore electrolytic seawater chlorine system
Offshore Electrolytic Seawater Sodium Hypochlorite generator system CHINA&UAE
Sodium Hypochlorite generator system CHINA&UAE
Features:
The Bluewav® series of offshore electrolytic seawater chlorine production systems are basically skid-mounted and integrated. The complete system adopts a pickling-free concentric circular tube (CTE) electrolytic cell, which can avoid the use of hydrochloric acid in the offshore state and eliminate the tube-sheet electrolysis. Troubles and worries caused by pickling of tanks and hydrochloric acid storage.
Special designs can be provided according to the relevant design standards and certification requirements of third-party certification bodies such as DNV-GL, BV, ABS, etc. For details, please consult our engineers.
Summary of the principle of sodium hypochlorite generator
The main reaction process of sodium hypochlorite generator electrolysis can be expressed by the following equation:
NaCl+ H2O = NaClO + H2↑
Electrode reaction: anode: 2Cl--2e- → Cl2 cathode: 2H2O + 2e- → H2 + OH-
Solution reaction: 2NaOH + Cl2 → NaCl + NaClO + H2O
The electrolysis process of the electrolytic seawater type sodium hypochlorite generator is an electrochemical reaction process, which uses seawater and electricity as raw materials to make sodium hypochlorite solution. Although the chemical principle is simple, there are many technical indicators that affect the economy. Therefore, the design of the electrolysis electrode of the sodium hypochlorite generator should consider various factors, according to the compact and reasonable structure, energy-saving operation, convenient operation and maintenance, high operational reliability, and long equipment life. And other characteristics to design and manufacture. The sodium hypochlorite solution is accurately dosed, safe to operate, easy to use, easy to store, non-toxic to the environment, and there is no air leakage, and it can be dosed under any environmental working conditions.
Design Features
1. No pickling
Unlike other forms of electrolytic seawater chlorine production systems, the concentric circular tube electrolyzer is designed specifically for offshore industrial applications and does not require any pickling during its operation. The concentric circular tube electrolyzer adopts the design of inner and outer double titanium tubes. The titanium tube is coated on one side. The seawater passes through the gap in the middle of the concentric circular tube electrolyzer. The cathode and anode form a circuit loop through the conductivity of the seawater to produce electrolysis.
2. Extremely harsh environment
The framework of the offshore electrolytic seawater chlorine production system adopts profiled steel shot blasting, pickling, galvanizing and anti-corrosion paint, and top paint spraying process. The electrical junction box and control cabinet are made of 316L stainless steel, which can withstand long-term wind and sun exposure. Rain and salt spray corrosion and other extreme harsh environments.
3. Explosion-proof
The complete set of equipment can be classified according to the level of the corresponding hazardous area, and carry out the relevant electrical, motor, control, power distribution and explosion-proof treatment of the rectifier transformer to adapt to the application and installation of different hazardous area levels.
4. Compact design
In view of the fact that the usable area of the offshore environment is not as large as the total usable area of the land-based electrolytic seawater chlorine production system, Bluewav Industrial and SESPI have many years of experience in the design of offshore platform electrolytic seawater chlorine production system and engineering cases. The company designed offshore complete electrolytic seawater chlorine production system adopts a unique integrated skid-mounted design, the equipment is compactly arranged and can meet the required electrolysis process requirements.
System composition
Sea water filtration system |
The seawater is filtered to micron level to prevent large particles from entering the electrolyzer group and affecting the electrolysis process. |
Electrolyzer group |
The electrolytic cell group is the core unit of the whole set of equipment. The electrolytic cell group adopts titanium-based ruthenium and iridium rare metal oxide coating. The seawater passes through the electrolytic cell group through direct current catalysis to convert seawater's sodium chloride into sodium hypochlorite and hydrogen. |
Rectifier transformer |
Usually, a rectifier transformer in the form of a silicon controlled rectifier is used, the voltage is changed to the required voltage through the transformer, and then a thyristor is used for controlled rectification. The input AC power is converted into DC power and the positive and negative poles provide power source and output to the electrolytic cell. |
Storage and dehydrogenation tank |
The generated sodium hypochlorite solution and hydrogen enter the storage and dehydrogenation tank through the pipeline for temporary storage and dehydrogenation process. |
Dehydrogenation fan unit |
The wind unit generally adopts the1D+1Sform,which blows a large amount of air into the storage and dehydrogenation storage tank to dilute the produced hydrogen and provides a power source to discharge the diluted hydrogen to a safe discharge point. |
Dosing pump set |
Use corrosion-resistant centrifugal pump to output to the dosing point. |
Control System |
The central control system of the complete set of equipment is used to control the automatic start and stop of the complete set of equipment and coordinated control with the outside. |
Power distribution system |
Allocate power sources for motors and related electrical drive equipment. |
Optional accessories |
1. Seawater booster pump set 2. Electrical system solutions for explosion-proof areas 3. HAZOP(Dangerous feasibility analysis) meeting 4. Third-party certification |
Application field
Petrochemical |
Offshore platform |
Ship |
Ballast tank water treatment |
Subsea storage water treatment |
Specification
Electrolyzer form |
Bipolar - Concentric tube |
Accessories material |
ABS (or PVC), EPDM and titanium |
Anode substrate |
Titanium ASTM B 338 GR.1 or 2 |
Anode coating |
Rare Metal Oxide (MMO) |
Cathode substrate |
Titanium ASTM B 338 GR.1 or 2 |
Cathode coating |
N / A |
Bipolar titanium tube substrate |
Titanium ASTM B 338 GR.1 or 2 |
Bipolar titanium tube anode coating |
Rare Metal Oxide (MMO) |
Seawater flow |
≥5.6 m3/Hr |
Design liquid temperature of electrolyzer |
5 to 55 degrees Celsius |
Ambient temperature of electrolyzer design |
0 to 85 degrees Celsius |
Design pressure of electrolyzer |
10 Bar |
Flow Chart
Products Category
- Hypochlorous Acid Anolyte Generator
- Medical grade Neutral Anolyte HOCL Generator
- Sodium_Hypochlorite_Generator (Seawater)
- Sodium_Hypochlorite_Generator (Salt Water)
- High Concentration Sodium_Hypochlorite_Plant
- Strong Alkaline Water generator Machine china
- Alkaline ionized water machine electrolyzed Water ionizer Machine china For Drinking Water Plant
- on site chlorine gas generator china
- Chlorine_Dioxide_Generator
- Chlorine Liquefaction Refill Cylinder Line
- UV sterilization
- Seawater Electro Chlorination System Package China UAE desalination
- Automatic dosing system PAC PAM
- Reverse_osmosis_RO_system seawater desalination system
- Online Chlorine Concentration Meter Gauge
- Sodium Hydroxide Generator detergent caustic soda plant NaOH
- Chlor-alkali plant membrane electrolysis
Contact Us
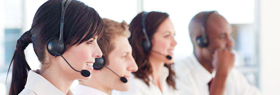
Name: Diana
E-mail: [email protected]
Skype: +86-15-22-27-71-011
WeChat: +8615222771011
Whatsapp: +8615222771011
Add: Office N.420D-C1 Tower Ajman,UAE